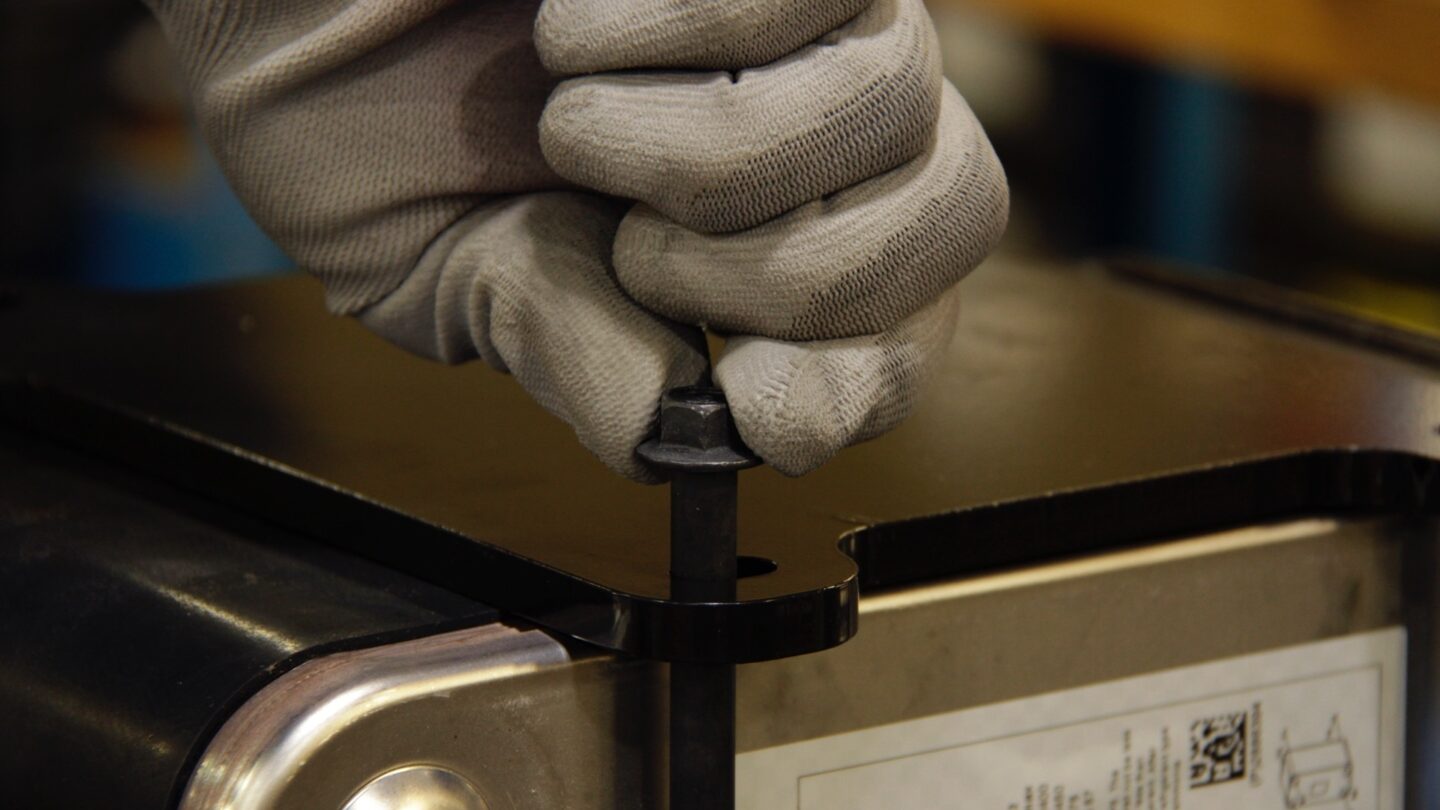
Assembly / Sub-Assembly
We do it right the first time.
Error-Proof Assembly and Sub-Assembly Solutions
MSW takes great pride in our quality control, as evidenced by our ISO 9001 and IATF 16949 certifications. We are your trusted source for error-proof assembly and sub-assembly solutions. In addition to our flexibility and adaptability, we have an exemplary record for accuracy, supported by our exceptional external audit scores year after year. Rigorous inspections, in-line Poka-yoke processes, and our state-of-the-art inventory management system combine to ensure every part is assembled and error-proofed according to customer specifications. Any component concerns that arise are traceable for our experienced quality professionals to investigate and resolve potential risks.
Capabilities
- Repeatable, Quality-Controlled Assembly Processes
- Failsafe Tooling Design and Manufacturing Processes to Ensure Product Meets Customer Specifications
- Vision Systems
- In-Line Mechanical Inspection
- Pressure Decay/Leak Testing
- In-Line Quality Verifications
- Proximity Validation Sensors
- Bar-code Printers & Scanners
- First & Last Piece Quality Inspection
- Processing Data Collection at the Part Level
- Full-Service Material Requirement Planning System
- Warehouse Management System with Real-Time Radio Frequency Data
- Management of Daily Planning, Staffing, Directing, and Controlling the Utilization of Available Resources to Move and Store Materials Into, Within, and Out of the Warehouse
- EDI Capable
- Ability to Collect Lot Traceability by the Bill of Material & Assembly Part Level
- Bar-code to Customer standards – Print, Serialize, Scan & Validate
- Lot Traceability – Manufacturing Assembly and BOM Component Level
- Utilizes the Following Practices & Controls:
- Cellular Manufacturing
- Safe Launch Planning
- Feasibility Studies
- Advanced Planning Quality Planning (APQP)
- Production Part Approval Process (PPAP)
- Lean Manufacturing
- Mistake Proofing
- Parts Per Million (PPM)
- Product Delivered Just in Time
To discuss your needs, contact us today for more information.
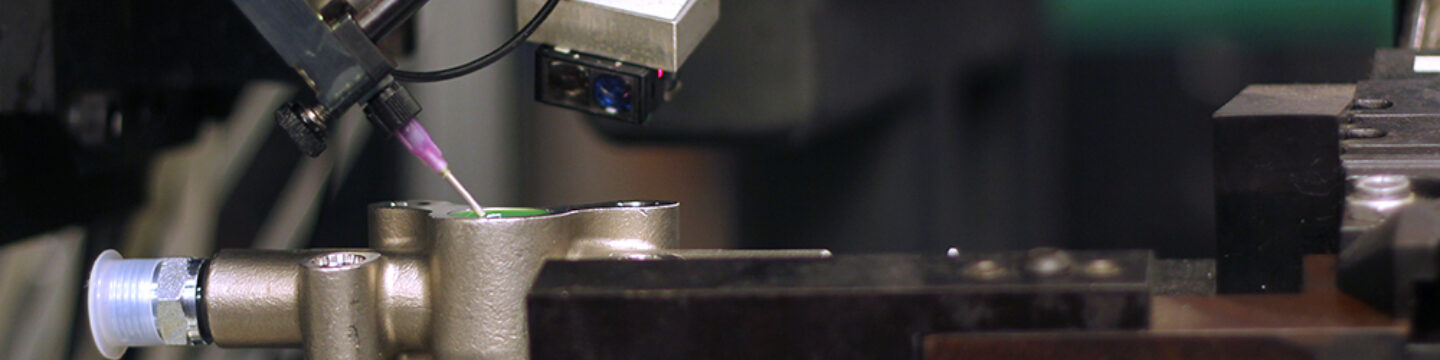