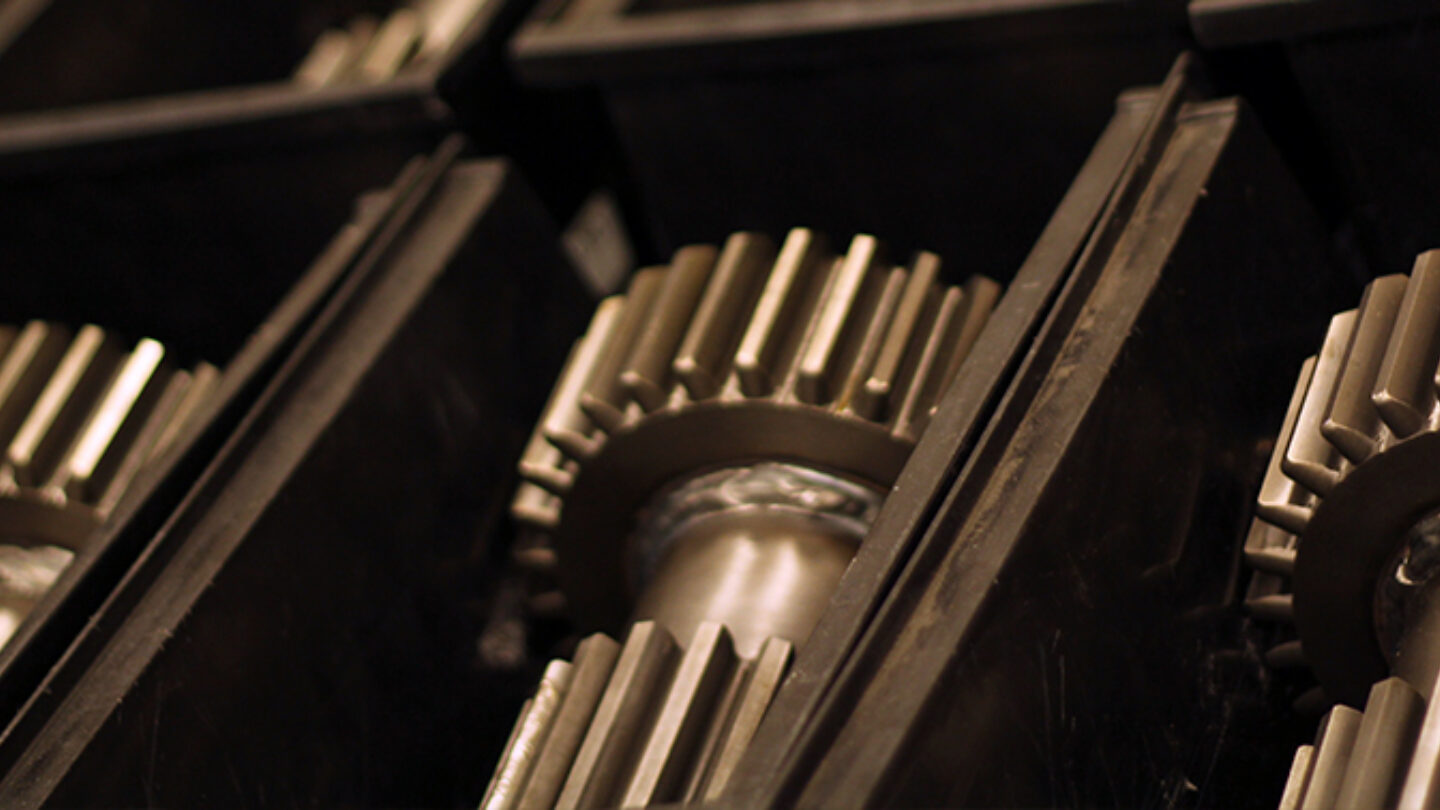
Sorting Services
Sorting is a critical part of the warehouse supply chain. Unfortunately, sorting is also a step that’s often overlooked, resulting in preventable inefficiencies. Using proper sorting protocols can help keep a warehouse much more organized and ensure the right parts are shipped to the right customers on time.
Parts sorting is the process of categorizing products and organizing them so they can be conveniently located. Most parts sorting processes involve segregating different parts according to characteristics such as size, shape, function, name, or whichever other attributes are relevant. Parts sorting is also sometimes called parts segregating. Each different organization may need to sort products according to different characteristics. For example, an automotive parts supplier and a computer parts supplier may need to sort their products according to different criteria.
Even though sorting sounds like a very simple concept, it is not always so simple in practice. Warehouses that frequently receive or ship large batches of products can easily become disorganized without effective sorting processes in place. That’s why sorting is such an important piece of the supply chain. It’s easy to neglect sorting, but a properly sorted warehouse is almost guaranteed to run more efficiently in the long run.
Fortunately, an organization that needs a more effective means of keeping warehouses sorted can rely on a sorting company to provide quality sorting services. Sorting services like MSW work with OEMs (original equipment manufacturers) to help sort and inspect parts, whether you need sorting services at your location, an MSW facility, or a customer’s facility. MSW’s sorting services are cost-effective, flexible, and provide a quick turnaround time.
A warehouse that is disorganized and not properly sorted can cause a huge loss of productivity. Poorly categorized parts can be difficult to locate and may become lost altogether. This can result in inconsistent recordkeeping and customers receiving late or incorrect parts deliveries.
Industrial Sorting Services
It’s very important for parts suppliers to find the best sorting services to help keep products organized. Large OEMs can benefit especially from the services of a 3rd party sorting company. Very large organizations that frequently handle sizable shipments are typically at a greater risk of lost parts or mishandled orders due to disorganization. Enlisting help from a third-party sorting company can enable large parts suppliers to keep their products categorized efficiently so shipments can be delivered correctly and on time.
Here are a few of the most prominent benefits of using industrial sorting services to keep your products organized:
Quality sorting companies can help original equipment manufacturers and other parts suppliers improve efficiency. There is no more need to search endlessly for parts that have been sorted into the wrong category or take a loss on parts that go missing due to improper sorting. Better sorting and organization can also lead to more efficient recordkeeping. An effective sorting process is one of the best ways to keep better track of inventory.
When a supplier uses industrial sorting services provided by a third-party company, the supplier’s customers can usually rest assured that shipments will arrive on time. When a large warehouse of parts is sorted ineffectively, it can result in errors that slow down shipping times. A properly sorted warehouse is much more likely to gather and send out shipments in a timely manner.
Poor sorting can also result in the wrong parts being shipped entirely. When a large supplier stores many different kinds of products, it’s imperative that they be sorted correctly, otherwise the supplier runs the risk of the wrong products being pulled for shipments. It’s important to be able to depend on everything being in its proper place. Industrial sorting services provided by third-party sorting companies can make it much simpler for OEMs or other large parts suppliers to stay organized and ensure correct shipments.
MSW’s sorting services are cost-effective and reliable. All sorting is processed through an adaptable project management system that enables clients to customize work instructions or receive detailed reports and summaries.
Warehouse Sorting Process
An efficient warehouse sorting process is one of the keys to keeping parts organized so orders can be fulfilled correctly and on time. In order to maintain effective sortation in warehouse environments, it’s necessary to have adequate warehouse sorting systems in place. Some organizations may implement and carry out these systems on their own. However, in many cases, a more effective solution could be to employ a third-party sorting company to handle the sorting process. This can ensure that sorting receives proper care and attention even if the organization does not have the in-house resources to devote to the task.
Developing an effective sorting process in warehouse settings generally revolves around ensuring the smoothest possible flow of products through the warehouse. Parts need to be categorized and sorted correctly every time so they can be pulled quickly and reliably when it’s time to put together a shipment for a customer. When a warehouse does not use proper sorting processes, it can make it much more time-consuming to find products and send out shipments — especially large shipments with a wide variety of products.
Sorting is one of the most vital of all warehousing techniques. As batches of products enter the warehouse, they need to be carefully categorized and filed accordingly. Each part will have a designated storage location, and it’s essential that every part finds its way to the correct shelf or bin. Every part that is incorrectly sorted will result in lost time somewhere else down the line when the problem needs to be corrected. Even worse, the error may go unnoticed, resulting in a customer receiving the wrong product. This can go beyond harming productivity in the warehouse and impact sales directly. When customers receive the wrong orders, it means they have to send the product back, and returns are not good for an organization’s bottom line or public image.
3rd-Party Inspection Services
Another important aspect of warehouse management is part inspection. Part inspection services are sometimes combined with sorting services because these two tasks often happen together. Quality inspections may take place at various points in the supply chain to create as many opportunities as possible to catch defective products. The sorting process is just one point at which inspection may occur.
Aside from sending shipments late or sending the wrong parts, one of the worst things an original parts manufacturer can do for its brand image is to send customers defective products. If a customer receives a defective product that was never detected by a quality inspection, they are not only missing the product they need, but now they have to go to the trouble of sending the part back and ordering a replacement. This is a customer service nightmare that could easily result in that customer choosing to order from a different supplier next time.
To help prevent situations like this example, parts suppliers can use third-party inspection services to assist with quality inspection — the same way they can use sorting services to achieve more effective sorting processes. Third-party quality inspections can provide assurance to OEMs that each and every part in their warehouses has been inspected and verified for quality. For example, in 2021, MSW’s quality inspections resulted in a defective part rate of 2 parts per million. Parts suppliers can take advantage of 3rd-party inspection services like MSW to reduce the chances of shipping out defective parts and losing business as a consequence.
Quality Control Inspection Services
Quality control is a vital part of the supply chain for original parts manufacturers. Putting effective product quality inspection protocols into place can help ensure that defective products are caught well before they end up in a customer’s shipment. Contacting a 3rd-party quality control company is one of the best ways to access reliable manufacturing inspection services.
Here are a few specific benefits of investing in the best quality control inspection services:
Greater efficiency - Third-party product inspection services can help make OEM supply chains more efficient. Quality inspections should be streamlined processes that don’t take up unnecessary extra time and provide reliable results.
Better brand image - More reliable quality inspections make it less likely that customers will receive parts that are defective. When customers get working parts every time, it looks good for the supplier. If a parts supplier’s quality inspections are lax and customers frequently receive defective parts, that supplier will be much less likely to get repeat business.
Higher sales numbers - A reliable quality control process ensures customers receive parts that work as intended. One of the most immediately obvious business results this can lead to is a higher bottom line. A more accurate inspection process means more customers get parts they are happy with on a consistent basis, which means they’ll keep ordering parts and maybe even spread the word about their positive customer experience.
Lower costs - Many third-party sorting and inspection companies can provide excellent QC inspection services at a low cost. MSW’s inspection services are flexible and cost-effective, making it an excellent choice for parts suppliers that need more practical sorting and inspection solutions.