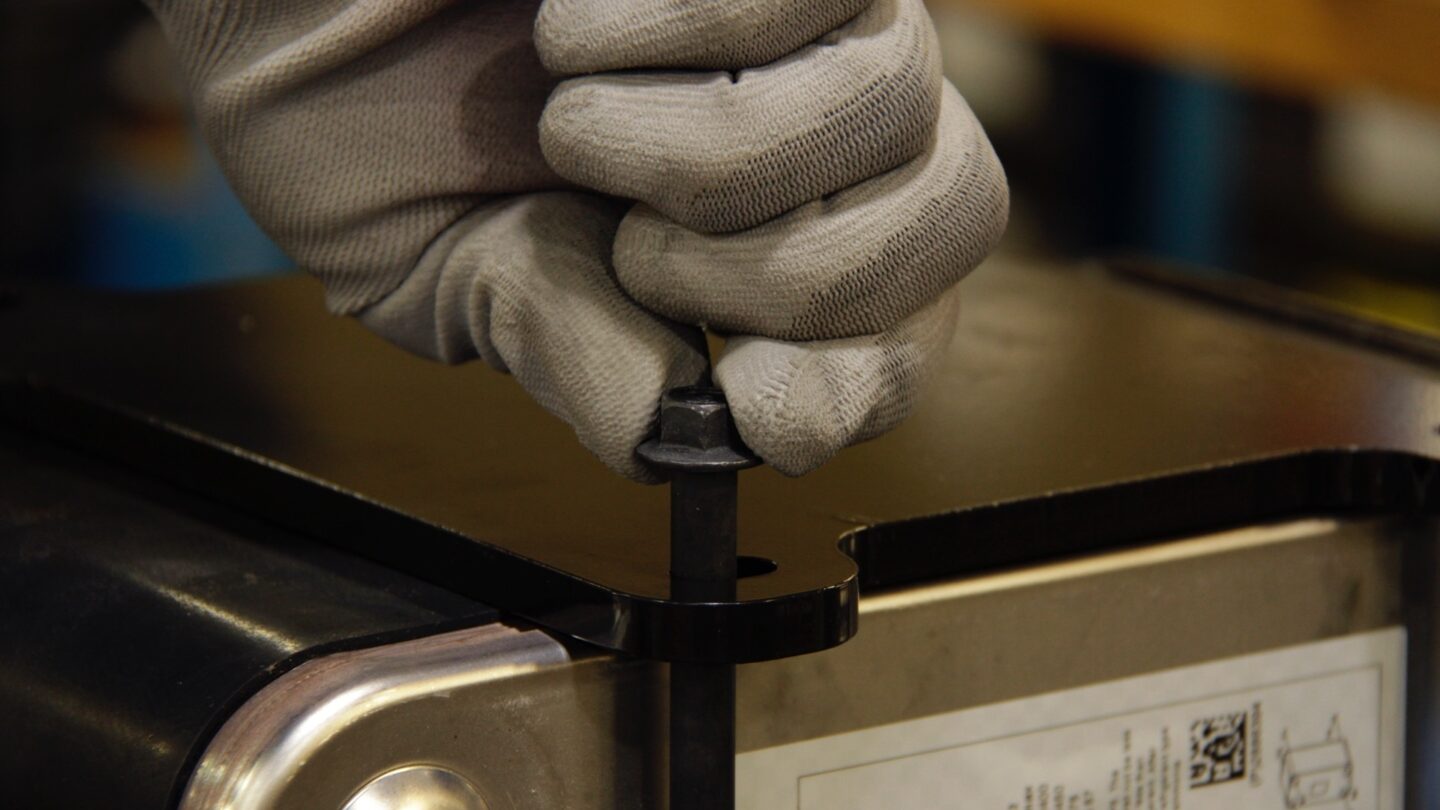
Metal Parts Assembly
In manufacturing and in other applications, metal parts assembly is the process by which metal parts are brought together to assemble a cohesive article, which may be a finished product or a subassembly. Metal parts assembly is highly crucial in several manufacturing processes that require the use of multiple metal components or parts. Assembly services, which sometimes support organizations and individuals by offering outsourced assembly capabilities, might be called upon to carry out the process of metal parts assembly.
When it comes to assembly, manufacturing is a realm within which it's often essential. In manufacturing, when multiple metal parts must be assembled, or when multiple metal components of a part must be assembled, several approaches can be taken, and several types of metal assembly can be required.
Additionally, a wide range of methods can be employed to assemble metal parts. These can include using fasteners, such as scream rivets, bolts, or clips, using welding techniques like arc welding, plasma welding, laser welding, spot welding, and brazing. Regardless of the type of metal parts assembly technique used, organizations that need metal parts assembly have a wide range of considerations.
Among these, organizations must often consider how they will carry out metal parts assembly, how they might manage storage associated with the production or manufacturing process, or should they opt to outsource metal parts assembly services, which metal parts assembly service they will entrust the process to. There are several reasons why an organization might outsource metal parts assembly, including scalability, flexibility, and efficiency.
Metal parts assembly is important in manufacturing across a range of industries. Some notable ones include aerospace manufacturing, automotive manufacturing, and computer and computer parts manufacturing. Any type of manufacturing that features metal components can require some metal parts assembly, though the complexity of metal parts assembly required can vary greatly.
For example, both manufacturing table lamps and aircraft manufacturing can require some level of metal parts assembly; however, in some cases, metal parts assembly in aircraft manufacturing may be significantly more complex, with more stringent quality requirements and more complex components involved.
Sheet Metal Assembly Techniques
Across different industries, sheet metal plays various roles. Sheet metal is a flat piece of metal that has been formed into a specific shape. Sheet metal can be made of different types of metal, including steel, copper, brass, and aluminum. These sheets of metal can be formed into a variety of parts and components, and sheet metal is often used to shape large metal objects, such as car bodies. Sheet metal can be formed and manipulated in a variety of ways. Sheet metal can be stamped, cut, pressed, bent, punched, and more.
A common application of metal assembly, sheet metal assembly is often used in a wide range of manufacturing, from simple home appliances all the way to complex construction components and machinery. Sheet metal assembly techniques can also vary greatly, as there are numerous applications for assembling sheet metal, numerous types of sheet metals that may be assembled, and various purposes for which sheet metal assembly might be carried out.
There are a number of different methods for joining or assembling sheet metal. These can range from welding and mechanical fastening to sheet metal clinching. This method is employed to assemble a certain component or product can vary based on factors such as cost-effectiveness or product requirements.
One such standard method for joining multiple sheets of sheet metal is welding. Welding is a process that involves utilizing high amounts of heat to fuse materials such as metals. Welding provides a high level of strength in joints and is commonly used in applications where joint force is essential. However, there are some potential reasons why welding may not be the method of choice in assembling sheet metal in some instances. Welding can cause issues such as heat-related deformation in some cases; in other instances, welding may simply be prohibitively costly.
While welding is a popular and common technique used in sheet metal assembly, several methods can be employed for joining sheet metal without welding. For example, clinching sheet metal is one way to join pieces of sheet metal together without welding them. The clenching of sheet metal involves using a press to create a joint between two pieces. This process can be not only versatile and helpful in a range of applications but also quick and efficient. As types of sheet metal joints and their uses can range greatly, so can the ways they are created.
Sheet Metal Assembly Process
As sheet metal is commonly used to create everything from appliances to large equipment and even buildings and vehicles, the importance of the sheet metal assembly process in several industries is difficult to overstate.
Sheet metal can range greatly in its uses, the materials that it’s made from, and its size. As such, methods for assembling sheet metal can also vary widely. As we’ve explored, there are a number of means that can be used to join pieces of sheet metal. It’s important to understand that in various capacities and applications, some of these methods may be considered more or less viable.
The sheet metal assembly process is crucial in various industries and across different stages in manufacturing. There are several components in the sheet metal assembly process, and from forming sheet metal to joining multiple pieces of sheet metal, sheet metal assembly can involve several varied approaches. Sheet metal formation is often necessary when creating single sheet metal components, and sheet metal assembly becomes essential when multiple metal components must be joined.
Sheet metal forming processes and applications can also vary widely; creating sheet metal can be done through various means, such as stamping, pressing, cutting, and bending. Types of sheet metal forming processes can vary in usefulness depending on the application.
Applications for sheet metal formation can include more extensive manufacturing processes, creating finished products, creating sub assembly components, and more. Sheet metal forming tools can consist of stamping machines, bending machines, presses, and others. Which device or sheet metal forming apparatus is best employed for a specific application can depend on the part in question, the requirements for the product or subassembly, and more.
The sheet metal assembly process is often essential to a more extensive manufacturing process. Numerous industries, including the aerospace manufacturing sector, automotive manufacturing, construction, and tech industries, rely on sheet metal assembly processes, enabling them to create products that utilize sheet metal.
Product Assembly Services
The assembly process is a crucial component of manufacturing, as it is the stage where all of the individual parts and components are put together to create the final product. Without a well-executed assembly process, the product may not function properly or may even be unsafe for use. This process involves a careful and deliberate approach, with each step being performed with precision and attention to detail. Additionally, the assembly process helps to ensure consistency and quality control, as each product is assembled in the same way to meet predetermined specifications. Ultimately, this process is an essential step in bringing a product to market that meets the needs and expectations of consumers.
There are times when assembly is best done by an outsourced service provider. Product assembly services are services that offer the capacity to assemble products. Assembly companies can range greatly in size and capabilities and serve several industries, such as the aerospace industry, the automotive industry, and the computer industry, among others. Assembly solutions can range in their complexity and may be more or less viable for specific organizations depending on the needs and requirements of the organization in question. Regarding the need for services in assembly, production stands out as an area where organizations often look for support.
Product assembly services can help organizations ensure that their manufacturing processes are carried out successfully by offering expertise, experience, human power, automation resources, supplies, equipment, or some combination of the above. Organizations that need to scale their production or manufacturing capabilities quickly and don’t wish to invest in on-premise equipment or additional staff may look to product assembly services to outsource certain vital operations. This can afford them scalability and flexibility; on-demand services can help organizations or individuals quickly make their products.
When it comes to whether or not to outsource assembly processes and rely on a product assembly service for support, there are several factors to consider. Manufacturers may feel everything from their needs and current capabilities to the services offered and their budgetary restraints. Some of the reasons why organizations might look to product assembly services include:
Access to expanded equipment: Product assembly companies may possess advanced equipment and machinery that enables them to assemble products more effectively or more efficiently.
Scalability: On-demand product assembly capabilities can enable organizations to scale production faster to meet their needs, especially if they are subject to rapid change.
Expertise: Product assembly companies might offer their expertise in product assembly and offer an enhanced ability to mitigate the risk of poor-quality manufacturing.
Flexibility: Product assembly services can afford organizations that utilize them some flexibility. In outsourcing certain product assembly processes rather than investing in resources needed to carry them out internally, organizations may allow themselves to change course more easily.