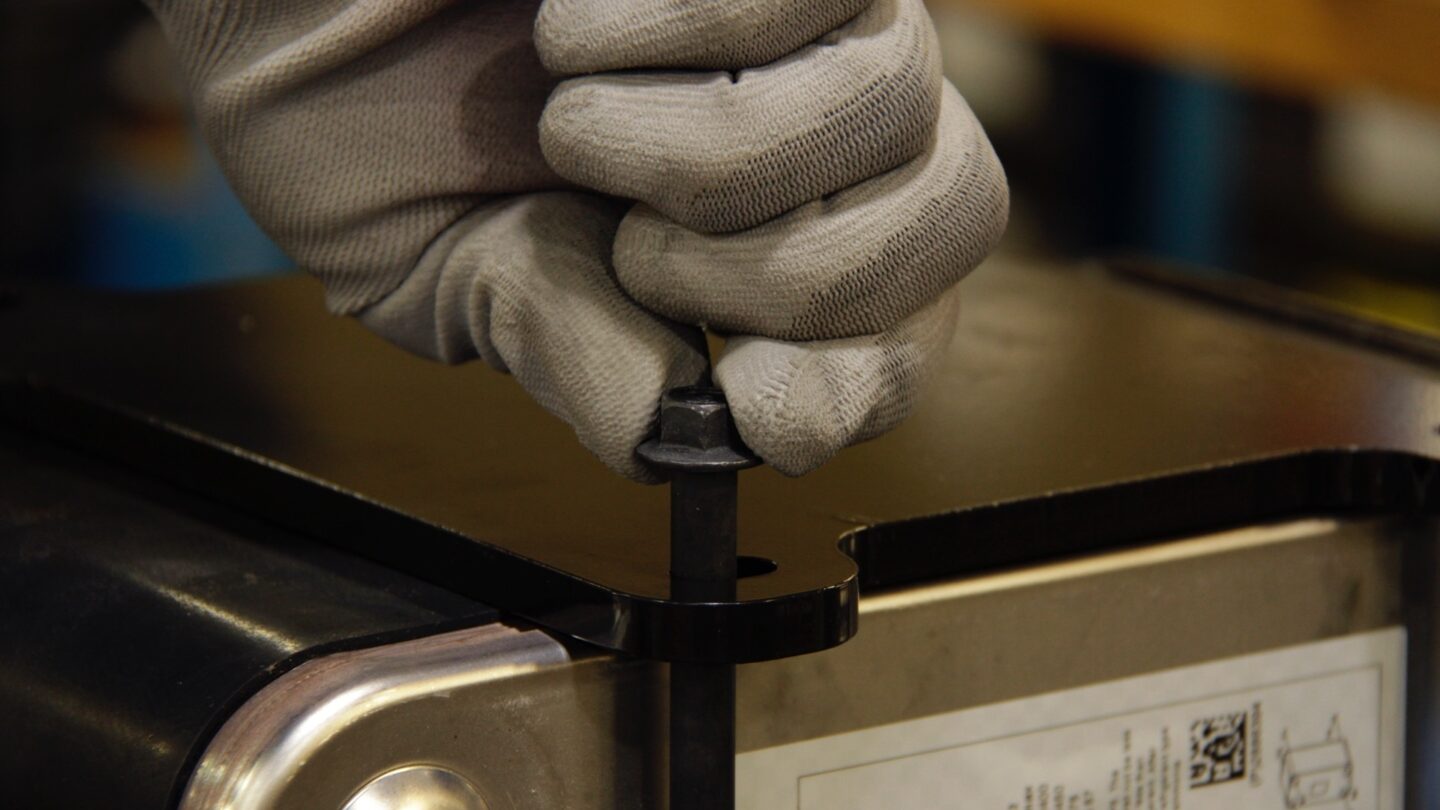
Insights into Automotive Sub-Assembly
Automotive sub-assembly refers to the process of combining several individual components or parts together to create a larger assembly or module within an automobile. A sub-assembly refers to the assembly of smaller components or parts into a larger component that can be installed as a single unit.
Some common examples of sub-assembly components include:
Engine Sub-assembly
This typically involves combining components such as:
Cylinder head
Engine block
Pistons
Connecting rods
Crankshaft
Parts are assembled together to create the engine module, which is then installed into the vehicle.
Transmission Sub-assembly
This includes assembly of components like your:
Gearbox
Clutch system
Drive shafts
Differential
These parts are combined to form the transmission module, which is then integrated into the vehicle's drivetrain.
Suspension Sub-assembly
This includes components like:
Shock absorbers
Struts
Control arms
Springs
These parts are assembled together to create the suspension module, which is then installed into the vehicle's chassis.
Electrical Sub-assembly
In this step, various electrical components are combined, including:
Wiring harnesses
Control modules
Switches
Connectors
These parts create a complete electrical system, which can then be configured to control various vehicle functions.
Dashboard Sub-assembly
The dashboard sub-assembly includes components like:
Instrument cluster
Infotainment system
Air conditioning controls
Switches
Many automotive components require sub-assembly before installation into the vehicle. This includes major systems like:
Engines
Transmissions
Suspensions
Electrical systems
Interior components
By pre-assembling these components as sub-assemblies, manufacturers can streamline production processes and facilitate easier integration into the final assembly of the vehicle.
Understanding Sub Assembly In Automotive Manufacturing
Sub-assembly manufacturing plays a crucial role in the automotive industry. The importance of sub-assembly manufacturing can be understood by considering the following aspects:
1. Improved Efficiency
Sub-assembly manufacturing allows for the simultaneous production of smaller modules, which can be assembled independently and in parallel with other manufacturing processes to optimize production flow.
2. Enhanced Quality Control
By producing sub-assemblies separately, manufacturers can focus on ensuring the quality of individual components before their integration into the final assembly. This enables better quality control measures and facilitates easier identification and rectification of any issues.
3. Streamlined Logistics
Sub-assembly manufacturing enables suppliers to deliver pre-assembled modules directly to the assembly line, reducing the need for extensive handling and component installation on-site. This streamlined logistics process improves supply chain management and reduces the risk of delays or errors during the final vehicle assembly.
4. Flexibility in Production
Sub-assembly manufacturing provides flexibility in the manufacturing process by allowing manufacturers to adapt and adjust production volumes based on demand. Different sub-assemblies can be easily integrated into vehicles based on specific customer requirements or vehicle configurations.
Examples of vehicle sub-assembly and truck sub-assembly include:
Vehicle Sub-assembly
A common example of vehicle sub-assembly is the production of engine modules. Various engine components such as the cylinder head or crankshaft are pre-assembled and tested as a sub-assembly.
Truck Sub-assembly
In the context of trucks, a typical sub-assembly is the cab module. The cab module includes components like the:
Dashboard
Steering column
Seats
Wiring harnesses
HVAC system
Manufacturers can simplify the overall assembly process by installing the complete cab module onto the truck chassis, reducing installation time and ensuring standardized quality.
The Process Of Automotive Sub Assembly
While the specific steps may vary depending on the sub-assembly being produced, here is a general overview of the automotive sub-assembly process:
Component Preparation
This first step involves preparing the individual components that will be assembled into the sub-assembly. Components are usually sourced from suppliers or produced in-house and then undergo quality control checks ensuring they meet required specifications.
Sub-Assembly Design
Sub-assemblies are designed to group specific components together for a particular function. Design considerations include:
Component compatibility
Ease of assembly
Adherence to safety and quality standards
Component Assembly
Skilled technicians or automated machinery perform the actual component assembly, fitting together components with fasteners, adhesives, or specialized tools.
Quality Control and Testing
After sub-assembly completion, quality control measures are implemented to ensure the sub-assembly meets the required standards. This may involve visual inspections, dimensional checks, functional tests, or performance evaluations. Any defects or issues are identified and addressed before the next stage.
Sub-Assembly Integration
Once the sub-assembly passes quality control checks, it is ready for integration into the final product. This may involve further assembly steps, such as attaching the sub-assembly to the vehicle chassis or integrating it into another larger module.
Documentation and Traceability
The entire time, documentation tracks the components used, assembly instructions, and quality control results. This ensures traceability and facilitates identification of any issues that may arise.
Important considerations and quality control measures during this process include:
Strict adherence to assembly instructions and specifications to ensure consistent quality and performance.
Thorough training of technicians and operators to ensure proper assembly techniques and minimize human errors.
Regular maintenance and calibration of assembly tools and equipment to maintain accuracy and reliability.
Implementation of visual inspection stations, quality control checkpoints, and functional tests to identify and rectify any defects.
Statistical process control techniques to monitor and control variation in sub-assembly manufacturing processes.
Continuous improvement initiatives to enhance sub-assembly efficiency, reduce waste, and optimize quality.
Benefits of Sub Assembly in Automotive Production
The benefits of sub-assembly in automotive production contribute significantly to improved production efficiency and quality. Here are some key advantages:
1. Streamlined Assembly Process
Sub-assembly allows for the consolidation of multiple components into pre-assembled modules, simplifying the overall assembly process. Instead of individually handling numerous parts, workers can focus on installing larger sub-assemblies into the vehicle, reducing assembly time and minimizing the risk of errors or missing components.
2. Enhanced Quality Control
Dealing with complex sub-assemblies improves quality control by enabling thorough inspection and testing at the sub-assembly level. Each sub-assembly can be evaluated for proper functionality before integration into the final product.
3. Improved Ergonomics and Worker Efficiency
Sub-assemblies can be designed to optimize ergonomics and ease of installation. By reducing the number of individual components handled during the assembly process, sub-assembly manufacturing reduces the physical strain on workers.
4. Supply Chain Management
Sub-assembly and kitting also play significant roles in effectively managing supply chains in the automotive industry. Suppliers can deliver pre-assembled kits directly to the assembly line, thus simplifying logistics
5. Cost Savings
By consolidating multiple components into larger sub-assemblies, manufacturers can reduce the number of individual parts and associated manufacturing processes. This leads to lower material and labor costs and potentially lower overall assembly line complexity.
Specifically, sub-assemblies and engine components at the sub-assembly level provides additional advantages in automotive production:
Challenges Of Automotive Sub Assembly
Automotive sub-assembly comes with its own set of challenges, including managing sub-assembly parts and dealing with broader industry challenges. Additionally, technology challenges in the automotive industry can also impact the sub-assembly process.
1. Managing Sub-Assembly Parts
One of the primary challenges in automotive sub-assembly is effectively managing the large number of parts involved. Sub-assemblies require coordination and synchronization of various components, ensuring their availability and proper sequencing during the assembly process.
2. Supply Chain Complexity
The automotive industry operates within complex global supply chains. Coordinating and managing the supply of sub-assembly parts from multiple suppliers, both domestic and international, can be challenging.
3. Quality Control and Testing
Sub-assembly components must undergo stringent quality control and testing to ensure they meet industry standards and specifications. Implementing quality control processes and conducting tests for sub-assemblies can be complex and time-consuming.
4. Technology Challenges
The automotive industry is experiencing rapid technological advancements, including the rise of electric vehicles (EVs) and autonomous driving technologies. Incorporating these technologies into sub-assemblies requires manufacturers to adapt and upgrade their production processes, equipment, and workforce skills.
5. Data Management and Integration
As the automotive industry embraces digitalization, managing and integrating data from various sources becomes crucial. Sub-assembly manufacturing involves gathering data on component specifications, quality control results, production metrics, and more. Learning to efficiently manage this data and integrate it into the overall production system can be a significant hurdle.
6. Training and Workforce Skills
The evolving nature of automotive sub-assembly necessitates a skilled workforce capable of adapting to new technologies and processes. Training employees to handle complex sub-assemblies and troubleshoot issues is essential.
Overcoming automotive industry challenges like these requires collaboration among manufacturers, suppliers, and technology providers.
The Role Of Sub Assembly In Supply Chain Management
The role of sub-assembly in supply chain management contributes to efficient supply chain risk management and overall supply chain integration. Let’s examine how sub-assembly fits into the supply chain management process:
1. Supply Chain Process
Sub-assembly is an integral part of the supply chain process. It involves the consolidation of components or parts into pre-assembled modules or sub-assemblies. These sub-assemblies can be manufactured by suppliers or in-house, depending on the supply chain strategy.
2. Supply Chain Integration
Sub-assembly enables better integration within the supply chain. By consolidating components into sub-assemblies, manufacturers and suppliers can synchronize their operations more effectively, allowing for improved coordination and communication and resulting in smoother production processes.
3. Supply Chain Risk Management
Sub-assembly manufacturing also plays a crucial role in mitigating supply chain risks. By pre-assembling components into sub-assemblies, manufacturers can reduce the number of suppliers involved in the production process and streamline procurement.
4. Inventory Management
Instead of managing a large number of individual components, manufacturers can focus on managing a smaller number of sub-assemblies. This reduces inventory complexity, optimizes storage space, and improves inventory visibility.
5. Just-in-Time (JIT) Manufacturing
Sub-assembly also aligns well with the principles of just-in-time (JIT) manufacturing. JIT aims to reduce waste and improve efficiency by delivering components (or sub-assemblies) to the assembly line exactly when they are needed.
6. Supplier Collaboration
Sub-assembly encourages collaboration and closer partnerships with suppliers. By relying on suppliers to provide sub-assemblies, manufacturers can establish long-term relationships and develop deeper understandings of each other's requirements, fostering mutual trust and better joint problem-solving.
By integrating sub-assembly into the supply chain process, manufacturers can achieve better supply chain integration and enhance overall supply chain performance.